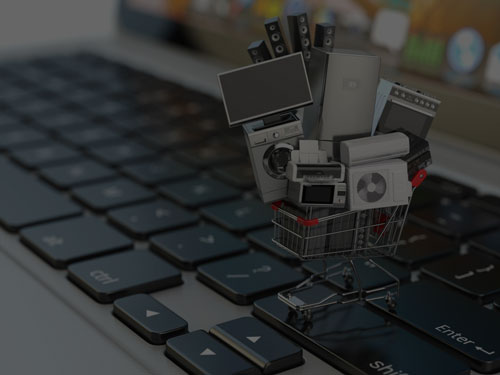

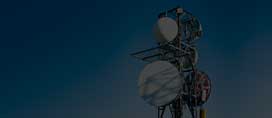

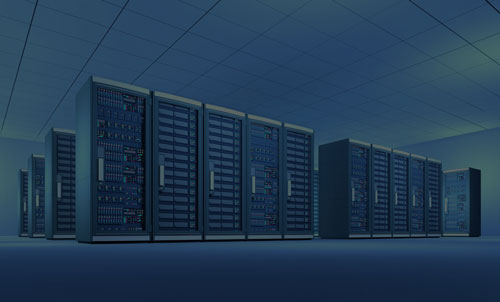

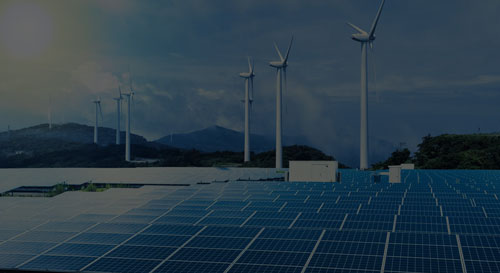

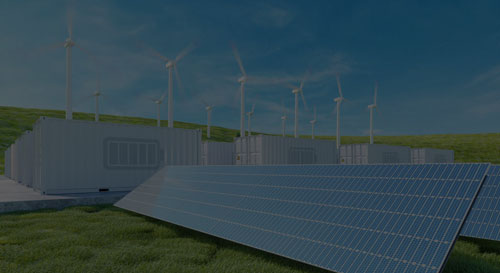

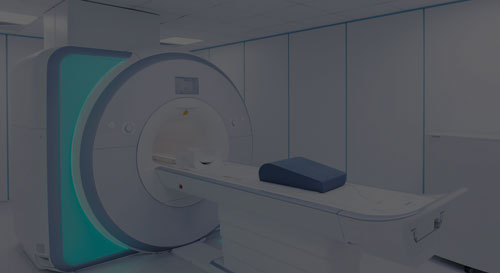

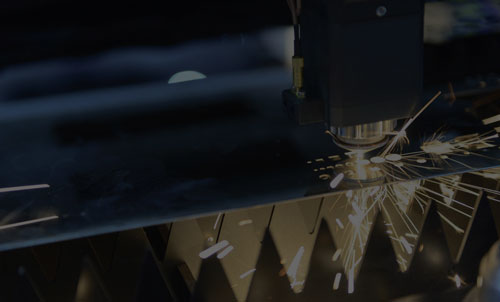
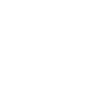
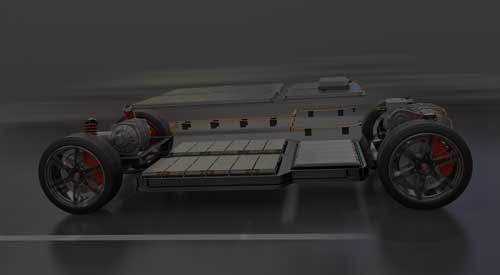

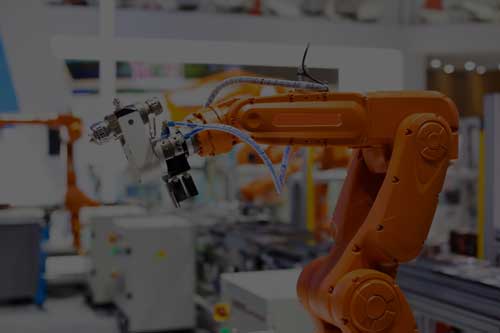

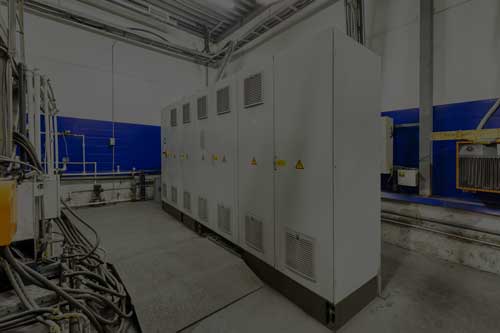
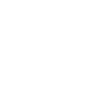
3C products are also called information appliances, which generally refers to computers, consumer communication and consumer electronics products. Various types of market demand is large. China has become the world's largest 3C product consumer market. The improvement of income levels also put forward higher requirements for the quality of electronic products. Merchants have launched higher configuration, higher performance, and better design products to meet consumers.
There are many factors that affect the quality of electronic products. Among them, heat dissipation is a factor that cannot be ignored. Especially after the "Samsung Battery Door" event was fermented in 2016, electronic manufacturers pay more attention to the heat dissipation performance and safety of the product. How can we ensure that the heat dissipation of electronic products meets rigorous design requirements?Planning thermal management issues at the beginning of the product design cycle is the best way to achieve the most efficient cooling solution. Hongfuhan Technology is a domestic first-class cooling technology service provider, which can provide cooling solutions for IT communication electronic products, involving: board (motherboard) cooling, CPU cooling, graphics card cooling, RF module cooling, RU cooling, game console cooling , VR cooling, industrial computer (machine) cooling, server cooling, central inverter air conditioning cooling, TEC cooling and other fields.
The goal of design simulation to design simulation:
PCB source temperature | ≤100℃ |
CPU temperature | ≤80℃ |
With the continuous development of modern communication technology, the power density of electronic and communication equipment is getting higher and higher, so the temperature caused by the equipment has risen sharply. The work life and performance of the equipment are closely related to Wen Yan. The heat management of electronics and communication equipment is facing huge challenges. How to solve the heat dissipation problem in a limited equipment space, how to control the component temperature within the allowable range, and how to ensure that the noise of the fan does not exceed the limit? Is choosing wind cooling or water cooling?
As the "heart" of the communication system, the 5G communication power supply determines the reliability of the entire system. In order to reduce and maintain cost benefits, improving the heat dissipation and reliability of the communication power supply is one of the main requirements of 5G communication power supply. For communication data, most of the existing equipment expansion methods are used to build 5G communication devices, which is often limited to the power space required for 5G communication power cabinets, and it can only be used in the original power cabinet. In these cases, the power supply can be used. In these cases The output power of the cabinet needs to increase significantly, which requires the communication power module, also known as the rectification module to increase the output power significantly when the volume is basically unchanged, that is, the power density increases.
However, due to the increased power density of power, the heat dissipation and insulation of power electrons became a bottleneck. Generally, the power device of the communication power supply is seriously heated, so it is necessary to heat dissipation through aluminum shells. Thermal conductivity tablets and heat -conducting gel can be well applied to the communication power supply to help solve the heat dissipation problem.
In 5G communication, the number of micro -base stations will increase significantly. Most of these small base stations will be installed in a closed space. Therefore, this type of communication power supply is intelligent. Appropriate heat dissipation solution
With the development of information technology, cloud computing and big data are gradually entering people's lives. As a node of the network, the server stores and processes 80% of the data and information on the network. It is similar to a general computer chassis, including processors, hard disks, memory, and system buses.
The needs of multiple media flow, cloud storage, data mining, analysis, and machine learning applications have been promoted to the demand for high -performance computing solutions, thereby increasing the number of CPUs and GPUs of the server to increase the speed of the processor. Due to the limited server volume, many high -power electronic components run in their long -term and high -load operations, and whether the heat generated by electronic components can be transmitted to the external stability of the server operation in a timely manner.
Servers heat dissipation usually requires several combinations of heat dissipation methods. In addition to active heat dissipation such as air -cooled and water cooling, in the heat dissipation solution, advanced thermal management materials, such as heat -conducting silicon film, heat conduction gel, etc. Help the connected, efficient heat dissipation path.
The inverter is also called power regulator. The process of converting DC electric energy into AC electric energy is called inverter, the circuit that completes the inverter function is called inverter circuit, and the device that realizes the inverter process is called inverter equipment or inverter. In solar power generation system, inverter efficiency is an important factor to determine the capacity of solar cells and batteries. Failure of photovoltaic inverter will lead to shutdown of photovoltaic system and direct loss of power generation, so high reliability is an important technical indicator of photovoltaic inverter.
Good heat dissipation of PV inverter is an important condition to ensure its high reliability operation. Therefore, heat dissipation simulation test at the beginning of inverter design has become the first consideration of PV inverter manufacturers.
The basic task of the energy storage system is to overcome the time or locality between energy supply and demand. There are two cases of this difference. One is caused by sudden changes in energy demand, that is, there is a peak load problem. The use of energy storage methods can be adjusted or buffered when the load change rate is increased.
Since the investment cost of an energy storage system is relatively lower than that of building a peak load plant, although the energy storage device will have storage losses, it can reduce fuel costs because the stored energy is the excess energy or new energy from the plant.The other is caused by reasons such as primary energy and energy source conversion devices, and the task of the energy storage system (device) is to balance energy output, that is, not only to reduce the peak of energy output, but also to fill the trough of energy output.
According to the regulations of the State Grid, the proportion of distributed generation such as photovoltaic and wind power cannot exceed 10% of the grid, and the energy storage system will be added if it is exceeded.
Because photovoltaic system and wind power system do not use energy storage system when they are connected to the grid, it will bring some adverse effects on the power grid, if the scale of wind energy and photovoltaic power generation system continues to expand and the proportion of photovoltaic power in the system continues to increase, these effects can not be ignored.
Through the analysis of the characteristics of photovoltaic power generation, we can know that the impact of photovoltaic power generation system on the power grid is mainly caused by the instability of photovoltaic power supply. In order to make the power grid more secure, stable and economical, it is generally required to install energy storage system. Therefore, the demand for energy storage system has increased in recent years.
The stable operation of the energy storage system is related to the security and stability of the power grid, so the major energy storage system manufacturers attach importance to its quality, and among the factors affecting the stability of the energy storage system, the heat dissipation performance is undoubtedly the most important.
Hongfuhan Electronics focuses on high-power heat dissipation and has rich experience in the development and manufacture of energy storage system radiators. Hongfuhan's thermal management engineers can provide heat dissipation solutions at the beginning of the design of energy storage systems. it can also optimize the heat dissipation performance of the energy storage system.
By accumulating rich thermal design data, Hongfuhan can provide accurate thermal simulation and thermal management test data.
In our normal use of medical equipment, due to the role of current, the internal temperature of medical equipment will be increased to different degrees. If the temperature exceeds the safe range under normal circumstances, a radiator or cooling device should be installed to ensure the normal operation of the equipment in use, which protects the service life of the equipment itself and improves the safety of the equipment. We can often see in the movie that when the electronic equipment and instruments are used beyond the load, the instrument will burn or even explode, so the radiator's role in the electronic equipment and instruments is beyond doubt. Therefore, when the medical equipment is maintained and repaired, the situation of the heat dissipation equipment should also be checked, so as to avoid the overheating of the circuit components caused by the abnormal work of the heat dissipation equipment.
With the continuous development of electronic assembly technology, the volume of electronic equipment is becoming smaller and smaller, the system is becoming more and more complicated, and the high thermal density has become an irresistible trend of development. In order to adapt to the development trend of The Times, the radiator is also constantly innovating, adapting to the pace of The Times novel heat dissipation methods also emerge in endlessly.
From imaging devices to surgical instruments, the powerful medical devices of the 21st century are impressive, thanks in large part to the increased computing power of microprocessors. For cooling engineers, however, these advances have come at a price. Equipment power is more and more large, the shape of the equipment is smaller and smaller, which also makes our radiator in the case of more and more power, in a smaller and smaller space to work, this is also the problem we will face.
Laser, as a strong artificial light source, is widely used. At present, the high-end projector has used a large number of laser as the light source, whether direct projection or reflection, the output brightness, color saturation, color gamut and so on are higher than the current ordinary light source.
The core of the laser projector is the laser generator, which inevitably produces a lot of heat when producing high-brightness and high-purity beams, and the laser generator is sensitive to temperature. Even if the temperature rises by one degree, it may lead to a straight decline in the brightness and purity of the beam, so the heat dissipation components of the laser projector are particularly important.
Fiber laser has become the focus of laser technology research because of its compact structure, high efficiency, good beam quality, stability and easy to use.
High power fiber lasers have important applications in basic research, national defense, industrial processing, medical and other fields.
The improvement of power and brightness and the expansion of working wavelength are two important directions in the development of laser technology, and they are also the core topics in the development of fiber laser.
With the increasing demand for fiber laser power, its large surface area and volume ratio can no longer meet the requirements of heat dissipation.
A large amount of heat accumulation will cause thermal damage to the key power devices, and even affect the system and performance of the fiber laser.
Therefore, it is necessary to adopt effective thermal control technology to heat the high-power fiber laser to meet the requirements of safe use.
Water-cooled heat dissipation has been the first choice for mature schemes.
Power battery is used to provide power for machines as a power source. It generally refers to the battery that provides power for new energy vehicles such as electric vehicles and electric trains. New energy vehicles refer to vehicles that use unconventional vehicle fuel as the power source, integrate advanced technologies in vehicle power control and drive, and form advanced technical principles, new technologies and new structures. New energy vehicles are favored due to their energy-saving and environmental protection characteristics, and are strongly supported by national policies. In order to implement the deployment and requirements of the State Council on cultivating strategic emerging industries and strengthening energy conservation and emission reduction, The central government allocated special funds to support the pilot of subsidies for private purchase of new energy vehicles.
New energy vehicles are mainly composed of battery drive system, motor system, electronic control system and assembly. The motor, electric control and assembly are basically the same as those of traditional vehicles. The biggest difference lies in the power source. The power battery pack is an important power source for new energy vehicles. Many new energy vehicle enterprises have increased their research and development on the power battery pack, trying to solve the technical bottlenecks of high cost, weak battery endurance and low charging speed of the power battery pack.
Schematic diagram of power battery pack and water-cooled plate simulation model:
The heat dissipation scheme is shown by taking 5 water-cooled plates as an example, with a total power of 1400W.
(1)cold plate A: 476* 134.4,souce size:179.2*134.4;
(2)Light red is the hot area,136.5W/each,total 273W;
The diagram shows the water flow distribution. The lower cover plate is 3.0mm thick, the upper cover plate is 4.0mm thick, and the middle fin is 3.0mm
Fin thickness 1.0, spacing 3.0mm, fin length 164mm, totoal 22fins;
(4)The middle cylinder (D10) is the structural strengthening position (sealed after screw fixing).
(1)cold plate B: 476* 57.4 souce size:177*44.3;
(2)Light red is the hot area,44.5W/each,total 89W;
(3)The diagram shows the water flow distribution. The lower cover plate is 3.0mm thick, the upper cover plate is 4.0mm thick, and the middle fin is 3.0mm
Fin thickness 1.0, spacing 3.0mm, fin length 165mm, totoal 9fins.
(1)cold plate C:670*240 souce size:663*180;
(2)Light red is the hot area,total 676W;
(3)The diagram shows the water flow distribution. The lower cover plate is 3.0mm thick, the upper cover plate is 4.0mm thick, and the middle fin is 3.0mm
Fin thickness is 1.0, spacing is 4.0mm, fin length is 610mm, 7 * 4=28fins.
Schematic diagram of heat dissipation simulation results of water-cooled plate of power battery pack:
(1)Schematic diagram of velocity diffusion degree in the middle section of water-cooled plate:
(2)Schematic diagram of pressure diffusion degree in the middle section of water-cooled plate:
(3)Schematic diagram of temperature diffusion degree in the middle section of water-cooled plate:
(4)Simulation diagram of temperature diffusion degree of water-cooled plate:
Summary of simulation data for cooling solution of water-cooled plate of power battery pack:
(1) Cooling medium: 50% ethylene glycol and 50% water, flow rate 10L/min, 25 ˚ C;
(2) The outlet water temperature is 27.3 ℃, and the water cooling temperature difference is 2.3 ˚ C;
(3) The maximum temperature of the radiator is 29.3 ˚ C;
(4) # 1 differential pressure 19200Pa, # 2 differential pressure 19700Pa, # 3 differential pressure 4300Pa;
(5) The overall differential pressure of the module is 19200 * 2+19700 * 2+4300=82100Pa.
Industrial control, namely industrial automation control, mainly refers to the use of computer technology, microelectronics technology and electrical means to make the production and manufacturing of the factory more automatic, efficient, accurate, controllable and visible. As the carrier of industrial control, industrial control machine needs high stability and special property requirements of continuous work.
The heat dissipation demand of industrial personal computer also needs to be efficient and stable. Poor heat dissipation can easily lead to machine failure or system instability, which has a bad impact on the industrial production environment. According to the characteristics and requirements of the industrial control industry, our company has adopted many fanless cooling solutions according to different customer system structures.
In this case, it is a customized motherboard. There are many components on the motherboard, and there are many components around the chip that are higher than the chip surface. This requires consideration and corresponding avoidance when designing the heat sink to avoid the heat sink from contacting the motherboard components or not contacting the chip surface.
As shown in the figure above - thermal simulation heat dissipation diagram of industrial control equipment solution
Application in Renewable Energy Field – Photovoltaic Inverter/SVG/Wind Power Converter
Devices based on high-power electronic devices such as photovoltaic inverter / wind power converter / SVG often work in harsh conditions and have high requirements for equipment heat dissipation.
Static Var compensator (SVC) is an important device to comprehensively deal with voltage fluctuation, flicker, harmonics and voltage imbalance.
SVG is a new type of static reactive power compensation device which is more advanced than SVC. It is an important part of flexible AC transmission system (FACTS) technology and customized power (CP) technology.
Both of them have been widely used in power transmission and distribution system: long-distance power transmission, urban secondary substation (35/110kV), electric arc furnace, mill hoist and other heavy industrial loads, regional power grid, photovoltaic power supply, wind farms, electric locomotive power supply and other fields.
SVG is a high heat element, which needs to cooperate with a radiator with excellent heat dissipation performance in order to ensure other stable operation and increase service life.
The SVG heat dissipation design requirements are as follows:
ambient temperature: | 40℃ | Style and model: | R4D560-AQ03-01 |
Altitude: | 3000m | Overall temperature requirements: | <35℃ |
Assumed IGBT model: | Infineon IHV IGBT,1250W/pcs,共2pcs, Resistor body:100W,total 2600W。 | Heat dissipation medium model: | I0.2mm ; K=4W/m*K |
Module power and quantity: | 7个,Total power :2600*7=18200W |
Layout diagram of heat source of SVG radiator monomer module: overall and partial diagram of cabinet:
Main parameters of SVG radiator design scheme:
The radiator size is 400x380x100mm, and the heat pipe layout is specially designed;
Heat conducting silicone grease is used between the heating element and the radiator;
Customized heat pipe with wall thickness of 1.0MM is used to ensure heat dissipation efficiency;
8 9.5 mm heat pipes at the bottom adopt the round pipe into the groove and flattening process to ensure the heat dissipation efficiency;
In thermal analysis, the thermal conductivity of Epoxy is adjusted to the data corresponding to the operating limit temperature to ensure the consistency between the simulation and the actual;
All aluminum bonded radiator is adopted;
The unit weight of the product is about 22.6Kg;
AL5052 is used for FIN sheet at the bottom of the plate; thermal conductivity: 138 w / m ^ 2 K;
The radiator fan parameters are:
Ebm peak 560 fan, model: R4D560-AQ03, data are as follows:
Schematic plan of radiator type:
Bonded fin+8 heat pipe design
Schematic diagram of radiator air inlet and outlet simulation:
Air flow simulation diagram:
Radiator simulation data summary:
item | Maximum temperature ℃ | Inlet wind speed m/s | Thermal resistance value C/W | The simulation data of radiator shows that the temperature is below 75 ℃, and the temperature rise is less than 35 ℃, meeting the customer's requirements. |
module1 | 74.56 | 5.4 | 0.0133 | |
module2 | 5.39 | 0.013 | ||
module3 | 74.52 | 5.4 | 0.013 | |
module4 | 74.72 | 5.36 | 0.013 | |
module5 | 74.56 | 5.56 | 0.013 | |
module6 | 74.63 | 5.58 | 0.013 | |
module7 | 74.43 | 5.58 | 0.013 |